An Overview of Compressor Discharge Temperatures
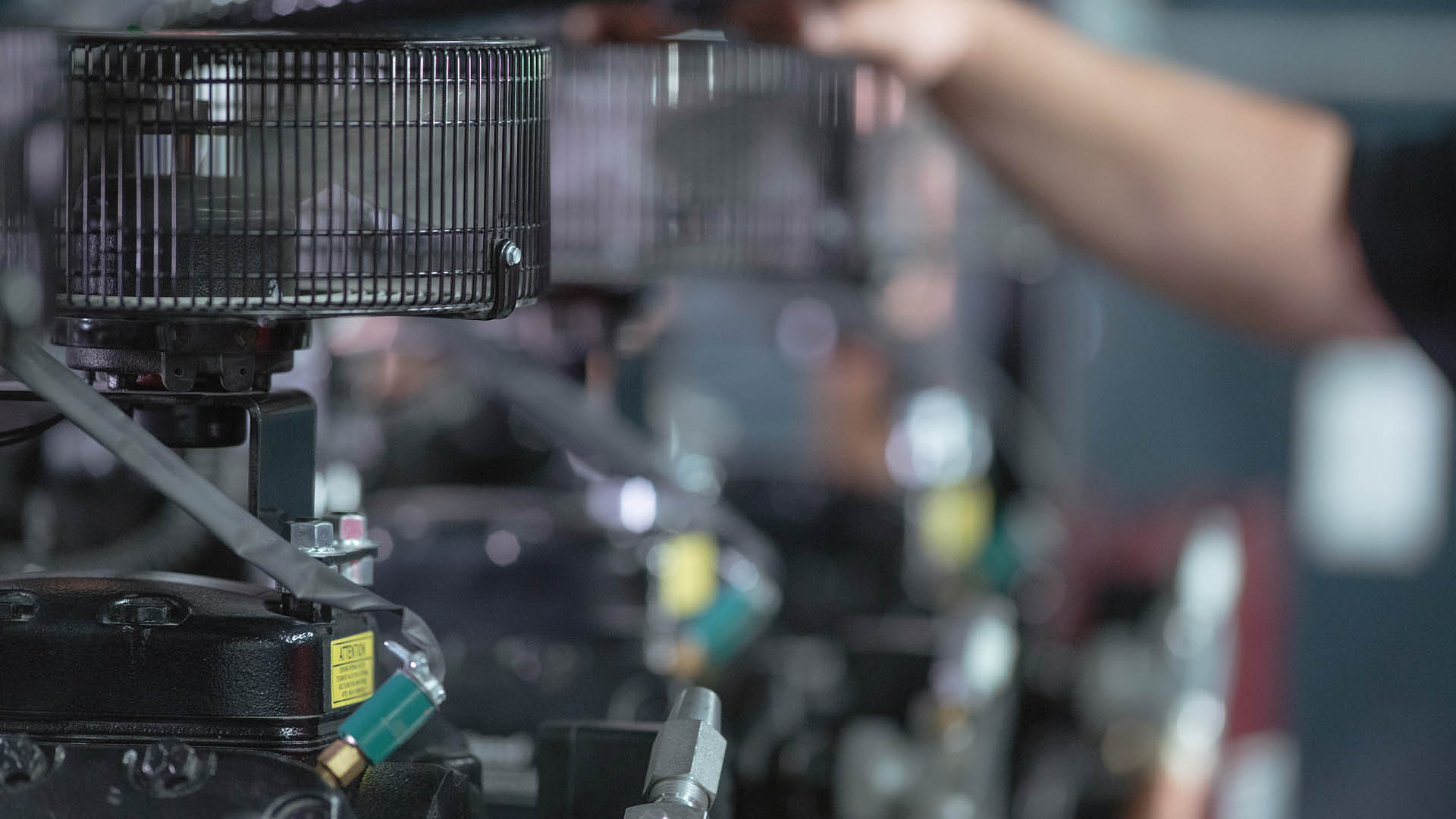
Measuring the discharge temperature in HVAC/R systems is essential for assessing the performance of the compressor. To do this, place an insulated thermistor or thermocouple on the discharge line approximately 3 to 4 inches from the compressor. The discharge temperature reflects the superheated refrigerant vapor's temperature.
It's important to note that since the discharge temperature represents a superheated vapor, there is no pressure/temperature relationship. Therefore, a pressure gauge cannot be used for this measurement. Pressure gauges are only applicable when determining a saturation temperature, such as during evaporation or condensing processes.
Monitoring Compressor Discharge Temperature
Monitoring Compressor Discharge Temperature
Monitoring the compressor’s discharge temperature is crucial as it reflects the internal conditions of the compressor. While the hottest part of the system is the back of the compressor’s discharge valve, it is not accessible for measurement. Therefore, the best alternative is to measure the temperature at the compressor's discharge line. Keeping a close eye on this temperature helps ensure optimal performance and prevent potential issues in your HVAC/R system.
The maximum allowable discharge temperature for any compressor is 225 degrees F. Exceeding this limit can lead to system failures caused by worn rings, acid formation, and oil breakdown. If the discharge temperature reaches 225 degrees, the actual discharge valve will be approximately 75 degrees hotter, bringing it to around 300 degrees. Most oils start to break down and vaporise at 350 degrees, leading to severe overheating issues. Since compressor overheating is one of the most serious field problems today, it is essential for service technicians to continuously monitor and maintain compressor discharge temperatures below 225 degrees to ensure optimal performance and prevent damage.
Some of the reasons for high compressor discharge temperatures are:
• High condensing pressures
• Low suction pressures
• High compression ratios
• High compressor superheats
Let’s explore the causes for these reasons.
High Condensing Pressures
High Condensing Pressures
High condensing temperatures lead to high condensing pressures, forcing the compressor to work harder and generate more heat during compression. This increased workload can result in reduced efficiency and potential system failures. Common causes of high condensing pressure include:
- Dirty condenser coils
- Burned-out condenser fans
- Broken fan belts
- Undersized condenser coils
- Overcharged refrigerant
- Presence of non-condensables in the system
- High ambient temperatures
- Recirculated air over the condenser
Addressing these issues promptly ensures optimal performance and longevity of your HVAC/R system.
Low Suction Pressures
Low Suction Pressures
Low suction pressures in HVAC/R systems can arise from various issues, leading to increased workload and heat of compression for the compressor. Common causes include:
- Undercharged systems
- Underfeeding TXV or capillary tubes
- Low evaporator heat loads
- End of the cycle
- Frosted evaporator coils
- Faulty evaporator fan
- Kinked suction lines
- Plugged suction-line or liquid-line filters
- Kinked liquid lines
- Plugged compressor inlet screens
Addressing these issues is essential to maintain optimal system performance and efficiency.
High Compression Ratios
High Compression Ratios
High compression ratios in HVAC/R systems can result from low suction pressures, high head pressures, or a combination of both. Increased compression ratios lead to higher discharge temperatures in the compressor due to the greater heat generated when compressing gases over a wider pressure range.
High Compressor Superheats
High Compressor Superheats
High compressor superheats often result from the evaporator being starved of refrigerant. Common causes include a restricted liquid line, undercharge, plugged filter-drier, kinked liquid line, or an underfeeding TXV or capillary tube.
In Conclusion
In Conclusion
Understanding and monitoring compressor discharge temperatures is crucial for maintaining the efficiency and longevity of HVAC/R systems. These temperatures reflect the cumulative heat from various sources, including latent heat from the evaporator, evaporator superheat, suction line superheat, heat of compression, and motor-generated heat within the compressor.
Proper management of discharge temperatures ensures that the system operates optimally, preventing potential issues and extending the lifespan of your equipment. By keeping a close eye on these temperatures, HVAC/R professionals can enhance system performance and reliability, ultimately delivering better service to customers.