Head Pressure Controls for HVAC 101
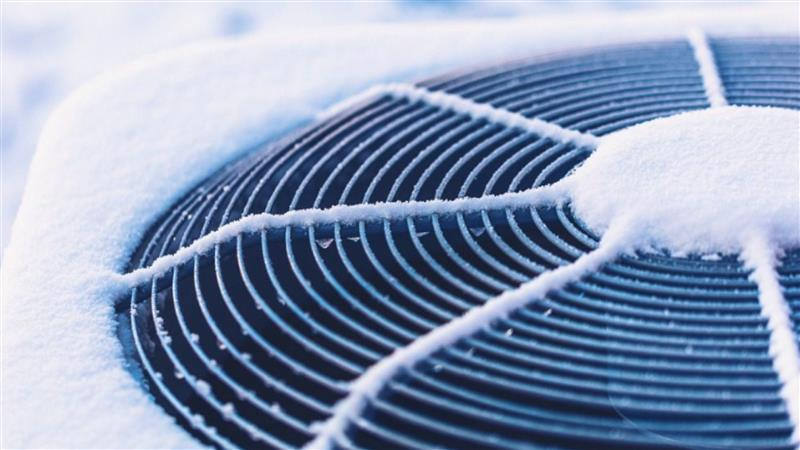
Maintaining consistent refrigerant pressure during colder weather is essential to ensuring HVAC system efficiency. In this post, we'll cover the basics of head pressure controls and how they ensure proper refrigerant flow in low ambient conditions. Without these controls, your system could experience problems such as poor evaporator performance and inconsistent cooling. We'll also explore methods like fan cycling and fan speed control to help manage head pressure and maintain smooth operation year-round.
When Do You Need a Head Pressure Control?
When Do You Need a Head Pressure Control?
Anytime you require cooling when ambient temperatures are low. There are a lot of applications that require year-round cooling, like server rooms, horticulture, mechanical rooms, and industrial process facilities to name a few. Some mini-splits are specially designed with head pressure control to operate as cold as -40°F. VRF has a range for heating, cooling and simultaneous, and these limits cannot be changed by adding an auxiliary head pressure control. In a roof top unit, the head pressure control taken care of by the economizer. However humid environments may want to review the range that the economizer and mechanical cooling would have, since there are limitations.
What Do Head Pressure Controls Do?
What Do Head Pressure Controls Do?
The purpose of head pressure controls is to maintain a consistent refrigerant pressure drop across the thermal expansion valve (TXV) during low ambient temperature conditions. Think about putting your thumb on the end of a garden hose. Your thumb is the TXV and you’re spraying refrigerant into the evaporator.
During low ambient operation (typically below 60°F), without head pressure controls, the high-pressure liquid refrigerant entering the TXV would drop to a level where the valve could no longer supply the evaporator effectively. Similarly, if you turned down the water flow on a garden hose, you’d be left with a weak spray. This reduced refrigerant flow causes the TXV to throttle incorrectly or ‘hunt’ for its equilibrium, resulting in alternating periods of starving and flooding the evaporator.
How Should Liquid Pressure be Maintained?
How Should Liquid Pressure be Maintained?
Maintaining high liquid pressure to the TXV is essential. This is achieved by reducing airflow across the condenser, which limits heat transfer from the refrigerant and keeps both temperature and pressure elevated. There are several methods to achieve this, including head pressure control valves, air dampers that restrict airflow over the condenser, or fan speed controls. In this post, we will focus on the fan speed and fan cycling options.
Types of Head Pressure Controls
Types of Head Pressure Controls
Fan Cycling Switch - $
Fan Cycling Switch - $
An on/off switch responds to pressure changes at the outdoor unit: it opens at low pressure, during a drop in ambient temperature and closes at high pressure, as the ambient temperature rises again. The advantages of this type of switch include low cost, ease of diagnosis, and the availability of replacements and retrofits. However, the downside is that pressure fluctuations can cause inconsistent system operation. This can place additional stress on the system, potentially leading to noise, and in extreme cases, leaks. When installed in the field, these switches are typically mounted on the liquid line service valve of the condensing unit.
Fan Speed Control - $$ to $$$
Fan Speed Control - $$ to $$$
A fan speed control senses head pressure using either a temperature sensor mounted on the condenser or a pressure transducer. The control system then adjusts the fan speed based on the head pressure—a drop in ambient temperature (or head pressure, if using a transducer) leads to a decrease in fan speed. As the fan motor slows, less air moves across the condenser, reducing heat transfer and stabilizing head pressure. The benefits of this method include maintaining more consistent pressure during operation, which results in a more stable evaporator temperature. However, the disadvantages are the higher initial cost compared to a fan cycling switch and the potential issue of motor compatibility with speed controls.
Head Pressure Control Applications
Head Pressure Control Applications
Ductless splits
Ductless splits
Most ductless manufactures have ECM driven condenser fans, which are slowed down in relation to ambient temperature. “Off the shelf” fan speed controls & fan cycling switches (i.e. ICM325, Johnson Controls P66 or P266, etc.) would not work with these motors. Ductless manufacturers will publish the lowest applicable operating temperature. Some ductless manufacturers, like Samsung and Daikin, will have low ambient specific units for year-round cooling.
Conventional Splits
Conventional Splits
A ball bearing PSC motor is generally the best choice, especially if the motor is explicitly labeled as VFD-ready (compatible with variable frequency drives). Manufacturers like Baldor and Marathon produce such motors. Standard sleeve bearing motors can also be used with ICM326 controls, as these controls maintain minimum fan and start-up speeds high enough to ensure proper lubrication.
Where Can You Use Head Pressure Controls?
Where Can You Use Head Pressure Controls?
Head pressure controls can be used in any space that has a year-round cooling load, such as electrical rooms, server rooms, MCC rooms and indoor grow facilities. These applications should all have some kind of low ambient consideration, as they will almost certainly be running during the winter. Depending on the criticality of the application, you should ask your RSL representative to select a piece of equipment accordingly. The more information we have regarding an application, the better we can serve you.
Contact Us
Contact Us
If you have any further questions about Head Pressure Controls, or if you have any other questions regarding refrigeration, you can contact the Refrigeration Support Team for further advice. Alternatively, you can contact your local branch for support.