CO2 Series: The Fundamentals of CO2 system operation
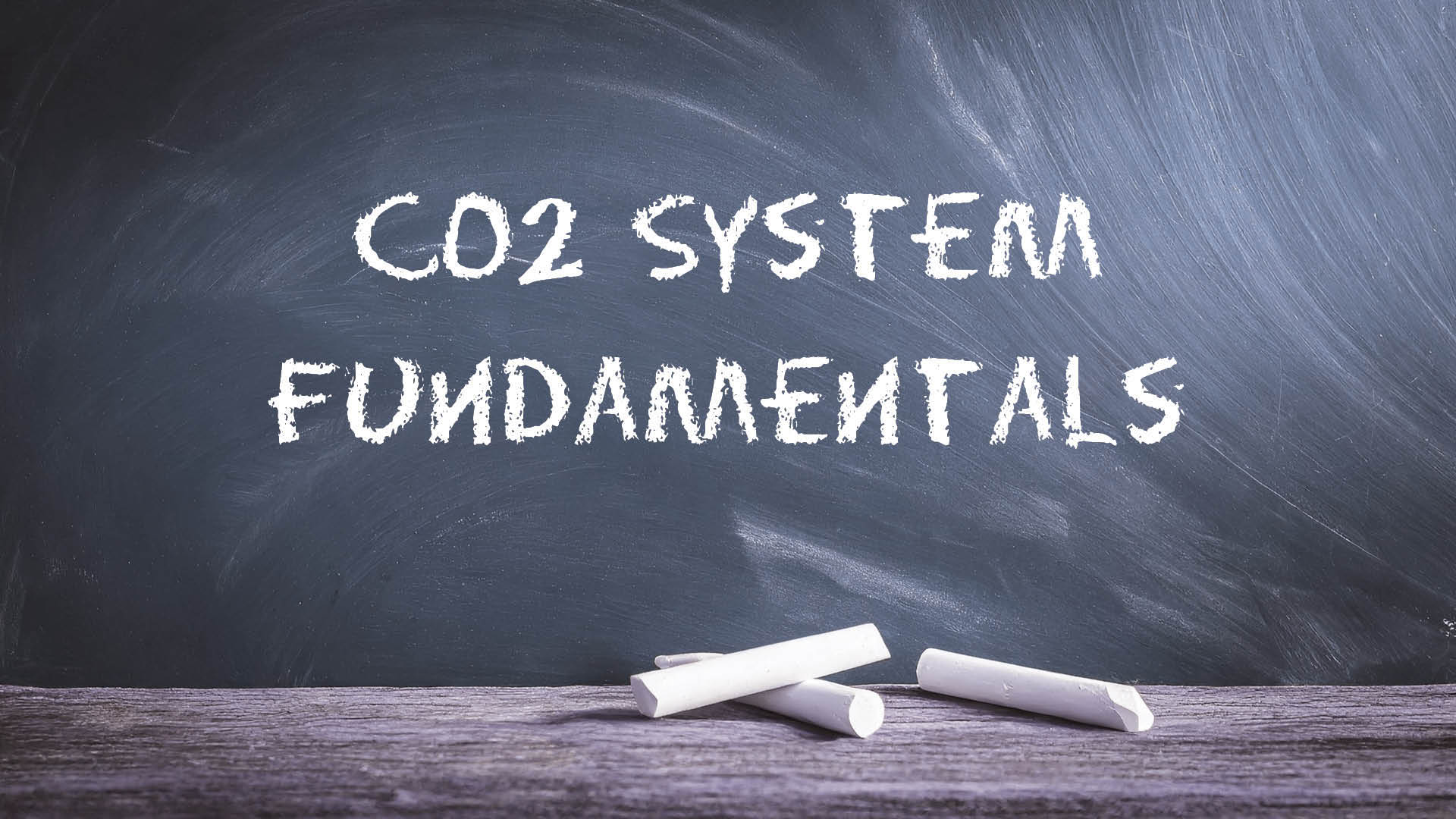
Because of R-744’s many distinguishing performance characteristics, CO2 transcritical booster system design can seem more complex to operate and service. Fortunately, system control technologies have evolved to manage nearly all aspects of operation and make it easy for operators to manage these complexities. Even so, end users and contractors should be aware of the basic principles when operating CO2 transcritical booster systems.
The Difference Between Subcritical and Transcritical Modes
The Difference Between Subcritical and Transcritical Modes
CO2 transcritical booster systems are designed to transition between subcritical and transcritical modes of operation. When R-744 is at saturation and below the critical point of 87.8°F, a system operates in subcritical mode. Above this refrigerant temperature, R-744 is no longer at saturation and the system enters transcritical mode. Unlike traditional HFC systems that have much higher critical points, CO2 systems could operate for extended periods while in a transcritical mode in a typical year. Managing high system pressures.
R-744 is a very dynamic refrigerant that reacts quickly to changes in pressures and temperatures. During the commissioning of a CO2 transcritical booster system, it's important to establish a stable baseline of performance. To achieve this, technicians should focus their efforts on the configurations of the gas cooler, high-pressure valve and flash tank, including:
- Controlling variable fan speeds
- Modulating the high-pressure valve
- Modulating the bypass gas valve
- Maintaining a consistent flash tank pressure
- Ensuring smooth compressor staging
Since all those aspects are managed by electronic controls, technicians will need to interface with these controls to bring the key system components into equilibrium.
Preserving CO2 System Charge During a Shutdown
Preserving CO2 System Charge During a Shutdown
Power outages and system shutdowns can have significant impacts on a CO2 transcritical booster system. In the event of an extended shutdown, CO2 transcritical booster systems are designed with pressure-relief valves in each zone to allow for the safe release of refrigerant.
During brief shutdowns, system pressures typically don't rise quickly enough to cause concern. A system's existing thermal inertia — from its flash tank, liquid line, MT and LT evaporators — will sustain proper pressures for a significant period of time. The temperatures outside and inside the building, among other factors, are likely to impact how long pressure will be sustained.
Another method for keeping pressures in check and preventing the release of system charge during an extended power outage is through an auxiliary condensing unit powered by a backup generator. The condensing unit typically utilizes a dedicated heat exchanger connected to the system's flash tank or receiver.
When the system is powered down, warm gas from the receiver naturally migrates through the cold heat exchanger, cools the flash tank vapor, condenses it into a liquid, and returns it to the flash tank at a colder temperature and lower saturation pressure. This helps to prevent the loss of refrigerant through pressure-relief valves.
Preventing Flooded Evaporators During a Power Outage
Preventing Flooded Evaporators During a Power Outage
CO2 transcritical booster systems are designed with specific strategies to prevent CO2 evaporators from flooding during a power outage. When the power drops in a system using a stepper-motor electronic expansion valve (EEV), the EEV typically will hold its exact position. Accordingly, CO2 transcritical booster systems are often designed to have a solenoid valve at the inlet of the EEV, which can be set to close upon losing power to help prevent flooding of the evaporator. Another strategy that would work is to install a battery backup on the case control to shut off refrigerant flow when necessary.
Systems equipped with pulse-width modulated (PWM) valves - which are in effect high cycle rate solenoid valves - are designed to automatically close to prevent liquid from flooding the evaporator, thereby protecting the compressor when power comes back on. Before the system is up and running again, service contractors should make sure that they clearly understand how the valves in each system will operate and/or close - and to confirm that any floodback mitigation strategies have worked as expected.
Contact Us
Contact Us
If you have any further questions about the fundamentals of CO2 system operation, or if you have any other questions regarding refrigeration, you can contact the Refrigeration Support Team for further advice. Alternatively, you can contact your local branch for support.