CO2 Series: CO2 Systems Design Strategies
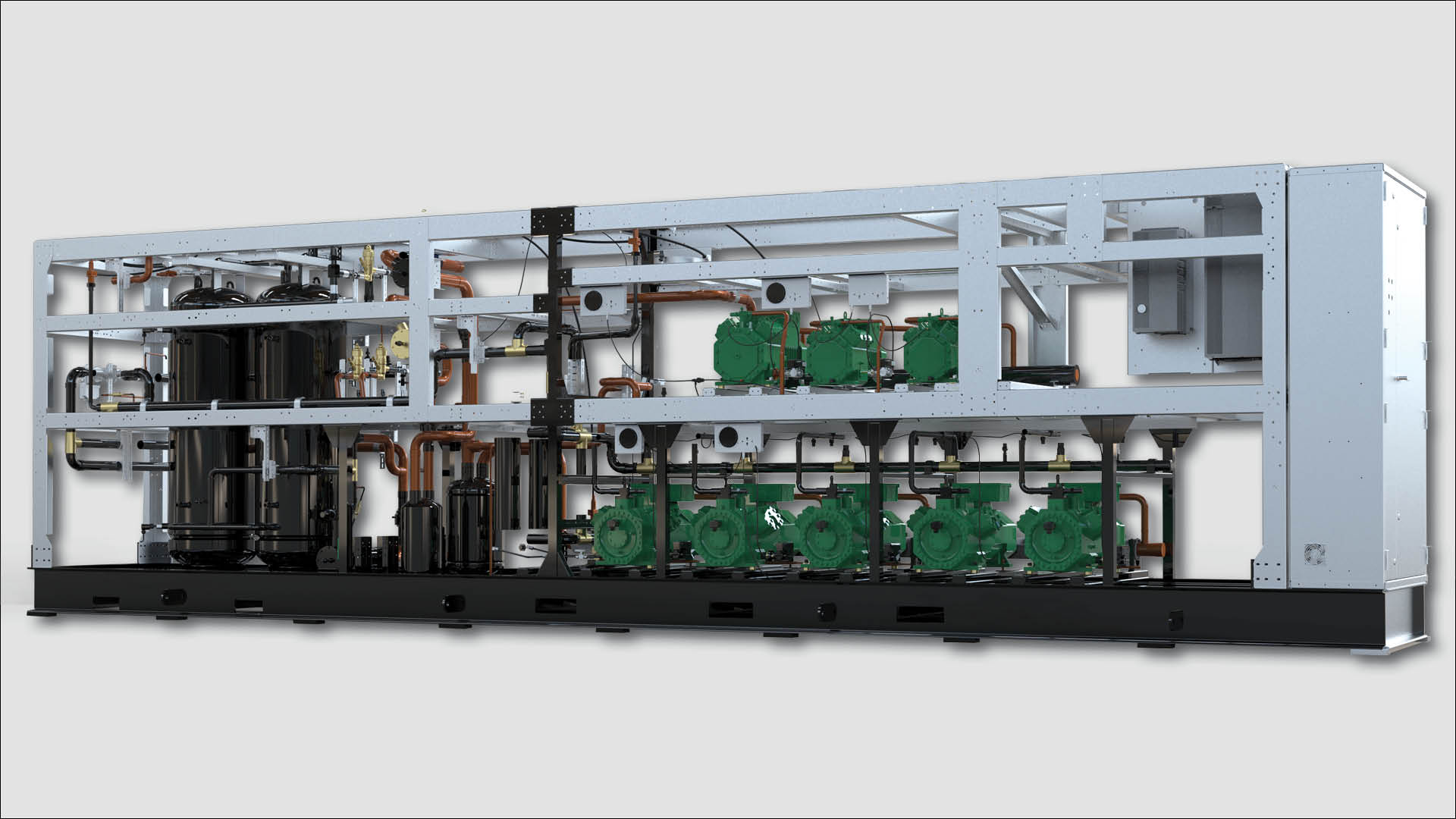
Refrigeration system designers have made tremendous strides in exploiting CO2’s unique properties into sustainable refrigeration architectures. Today, system design strategies have evolved into two primary architectures that differ greatly from traditional HFC-based systems.
CO2 Transcritical Booster System
CO2 Transcritical Booster System
CO2 transcritical booster systems are designed so that MT compressors discharge into a gas cooler, typically located on the roof of a facility. With system pressures potentially reaching 1,400 psi on a hot summer day, R-744 must be cooled before it can be condensed. Thus, refrigerant is circulated back into the building through a high-pressure valve, which drops the pressure to a useable state (550 psi) and deposits a refrigerant mixture of vapor and liquid inside the flash at 40°F equivalent saturation.
Next, the system circulates the 40°F liquid through insulated liquid lines to feed all the MT and LT cases and provide the cooling loads. The MT cases are equipped with an EEV, and the MT suction gas feeds the MT compressors. On the LT side where loads could be -20°F, the cases are also fitted with an EEV and are supported by a separate set of LT compressors that discharge into the MT suction group.
The system also utilises a bypass line that's designed to relieve the pressure on the flash tank. As ambient temperatures rise and fall, flash tank pressures can also fluctuate. Thus, the bypass line helps to release the excess flash tank pressure through a bypass gas valve and stabilise it to approximately 550 psi (pressure may vary based on system design), where it is directed into the MT suction group. In effect, the MT compressors are being fed by three sources:
- The total heat of rejection from the LT compressors
- The MT suction from the evaporators
- The excess flash gas via the bypass line
The system is called a booster system because the LT compressors are not going directly to the gas cooler, like they would a typical HFC system. Instead, the LT compressors discharge into the MT compressors, thereby allowing the MT compressors to boost the refrigerant to the gas cooler.
CO2 Cascade System
CO2 Cascade System
A CO2 cascade system offers an alternate architecture for retailers who want to deploy a low-GWP option but may not want a full CO2 transcritical booster system. In a CO2 cascade system, the high (MT) and low (LT) stages are completely independent of each other, except for one heat exchanger that connects them.
Typically, the high stage of a supermarket system would use a lower-GWP, medium-pressure HFC refrigerant, such as R-513A. Not only does it serve the MT loads, but it is also used to condense the CO2 in the low stage. In the low stage, CO2 is discharged, condensed in a condenser, and then recirculated for LT loads. R-744 is a very effective refrigerant for LT loads, and with a GWP of 1, it contributes to a cascade architecture that could meet many retailers’ sustainability objectives.
Leveraging Heat Reclaim
Leveraging Heat Reclaim
CO2 systems are excellent candidates for heat reclamation strategies. In fact, most modern CO2 systems utilise some form of heat reclamation - whether it's for providing heated air, hot water, or even heating slabs beneath freezers. Many retailers are capitalising on this opportunity to lower their emissions and reliance on fossil fuels.
In addition, the liquid quality of R-744 is not affected when head pressures are raised to generate more heating capacity. Instead, the flash tank or receiver is designed to keep refrigerant at a consistent pressure, even while head pressures may fluctuate while operating in transcritical mode.
Optimising the COP via the High-Pressure Control
Optimising the COP via the High-Pressure Control
When R-744 exceeds its critical point of 87.8°F, the refrigerant enters a supercritical phase where the relationship between pressure and temperature becomes uncoupled. To optimise the coefficient of performance (COP) in a CO2 transcritical booster system, we must understand the function of the gas cooler and the characteristics of R-744 as it enters this supercritical zone.
Below the critical point, the gas cooler acts like a condenser. Thus, R-744 exists in a predictable state of saturation - if you know the pressure, you can determine the temperature (and vice versa). In its subcritical state, the high-pressure control algorithm automates system pressures according to a specified sub-cooling setpoint.
Above 87.8°F, the pressure can change without having an impact on the temperature (and vice versa). System designers can take advantage of this phenomenon when optimising COP. When operating transcritical mode, the high-pressure control always seeks to maintain an optimal pressure setting for each gas cooler outlet temperature. Today's sophisticated high-pressure controls are continually adjusting gas cooler outlet pressures in transcritical mode to produce the most optimal BTU/W option.
Maintaining Energy Efficiencies in Warm Climates
Maintaining Energy Efficiencies in Warm Climates
The energy consumption of a refrigeration system is a key factor when evaluating its total cost of ownership (TCO). For a CO2 transcritical booster system, energy efficiency is dependent on many factors, including:
- The ambient temperature
- The humidity of the region
- The availability and cost of water
- The cost of peak demand changes
Among these factors, the goal of improving system energy efficiencies in warmer climates has become a major focus area for equipment manufacturers. Leading system design optimisation strategies typically include:
- Adiabatic gas cooler
- Parallel compression
- Mechanical sub-cooling
- Gas ejector
- Zero superheat control of MT evaporators
- Liquid ejector (annualised benefit)
Retailers must consider all these variables and strategies when they work with their equipment suppliers and design engineers to specify a CO2 transcritical booster system.
Adiabatic Gas Cooler
An adiabatic gas cooler utilises wetted pre-cooling pads outside the condenser coils to delay a CO2 transcritical booster system from entering into transcritical mode. When the ambient temperature reaches about 72°F, a water solenoid valve is energised, causing water to be sprayed along the top of the adiabatic pads.
As the water trickles down the pads, a condenser pulls air through these wetted pads, causing moist, cooler air to hit the coils. In turn, the condenser reacts to this cooler air and drops the temperature and pressure, making the system significantly more energy-efficient by operating at lower pressures.
Parallel Compression
Parallel Compression
In a CO2 transcritical booster system, parallel compression refers to the practice of adding a separate suction group that is “parallel” to the existing MT suction. Thus, instead of the bypass gas circulating from the flash tank to the MT suction as in a standard transcritical booster system, the parallel compressor suction group compresses excess flash gas and circulates it directly to the gas cooler.
This allows the parallel compressor to operate at a suction pressure of about 550 psi (the same as the flash tank), instead of the MT suction of 420 psi. The net effect of leveraging the higher suction pressure is achieving higher compressor capacity for less effort, which translates into a lower heat of compression and reduced energy consumption. Parallel compression is considered a foundational high ambient strategy with which other energy mitigation methods can be used in combination. When annualised in a typical environment, it can potentially save up to 10% in energy costs.
Contact Us
Contact Us
If you have any further questions about CO2 systems design strategies, or if you have any other questions regarding refrigeration, you can contact the Refrigeration Support Team for further advice. Alternatively, you can contact your local branch for support.